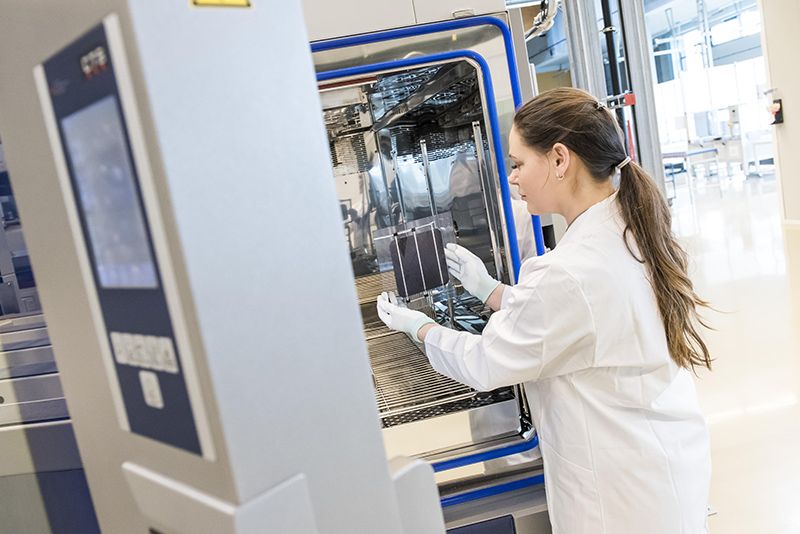
The Henn na hotel in Nagasaki, Japan, is not shy of trialling futuristic technology. It claimed to be the world’s first robot-staffed hotel in 2015 — but cut down on the automation after its robotic concierges frustrated some customers and didn’t reduce costs. Now, the Henn na is testing another attention-grabbing innovation: since December, its sign has been powered by a curved wall of prototype solar cells installed in the hotel’s grounds. Made by Polish start-up firm Saule Technologies, the cells exploit micrometre-thin films made from materials called perovskites, which in just a decade have shot from laboratory curiosity to bright new prospect for solar power.
Japan is not the only place where perovskite-containing solar cells have ventured outside labs in the past 18 months. Saule has hung them high on an office building near its headquarters in Warsaw; a leading British firm in the sector, Oxford PV, is testing them at a pilot production site in Brandenburg an der Havel, Germany; and the Chinese firms Microquanta Semiconductor and WonderSolar have been running field tests in the cities of Hangzhou and Ezhou. More than a dozen companies worldwide (see ‘Solar hopes’), a mixture of established electronics giants and start-ups, are hoping soon to sell panels made with perovskites. Dozens more are involved in making materials for the products, says Margareth Gagliardi, an analyst with BCC Research in Wellesley, Massachusetts.
For decades, slabs of crystalline silicon have dominated the solar industry. Other materials that can be layered in thin films, such as copper indium gallium selenide (CIGS) and cadmium telluride (CdTe), have captured less than 5% of the market, because it’s hard to make them as efficient or cheap as conventional solar panels. Perovskites could be a different story. They should be cheaper to make and seem impressively efficient at converting sunlight into electricity — in the laboratory, at least.
Not even the technology’s keenest advocates think that perovskite cells will quickly displace silicon, however. Instead, some firms are layering low-cost perovskite crystals on top of silicon to make ‘tandem’ devices that convert more of the Sun’s energy than either material alone. Oxford PV, for instance, intends to make tandems this year that it says will be one-fifth more efficient than top-end commercial solar panels. If rolled out across the industry, the total power output of solar panels made annually would leap by that same proportion. Further improvements should follow, says Chris Case, the firm’s chief technology officer. And that could help to accelerate the take up of a technology that still provides just 2% of the world’s electricity. “The world needs as much solar energy as we can get,” Case says.
Saule and other firms, meanwhile, aim to coat plastic with perovskite films to create lightweight, flexible products. Although less efficient, these devices could be used where heavy, glass-backed panels can’t, such as on top of cars, boats, aeroplanes, weak roofs, in rollable photovoltaic blinds or even sails that double as solar panels.
But there are still fundamental questions to answer about the new materials. It’s not clear whether perovskites will be durable enough to work through rain, wind, intense sunshine and freezing temperatures for the 25 years that silicon panels promise. Most perovskite devices contain lead, raising concerns about toxicity, and researchers are not convinced that efficiency records in the lab will translate to the commercial scale. Meanwhile, conventional solar panels have been getting ever cheaper and more efficient. That makes it hard for a new material to outperform them and accelerate efforts to combat climate change. “I wouldn’t put all my eggs in this basket for solving the world’s problems, but I also wouldn’t rule it out,” says Sarah Kurtz, a photovoltaics expert at the University of California, Merced.
Fishing for efficiency
At Oxford PV’s research laboratory, a 15-minute drive north from the University of Oxford, white-coated, hair-netted workers test gleaming black cells 1 square centimetre in size. They are exploring new material combinations that are more efficient at converting light to electricity. The type of finished product that they’re aiming for lies nearby on a bench: a large, perovskite-coated solar module the size of a standard silicon cell, 243 cm2, laminated between two sheets of glass. “We’ve measured hundreds of thousands of devices,” says Case.
Researchers have many options because ‘perovskite’ describes a large universe of crystal structures (see ‘Perovskites in the Sun’). The term originally referred to the mineral calcium titanium oxide (CaTiO3), which was discovered in Russia’s Ural mountains in 1839 and named after Russian mineralogist Lev Perovski. But the perovskites in solar cells have little in common with that mineral, just their ABX3 structure.
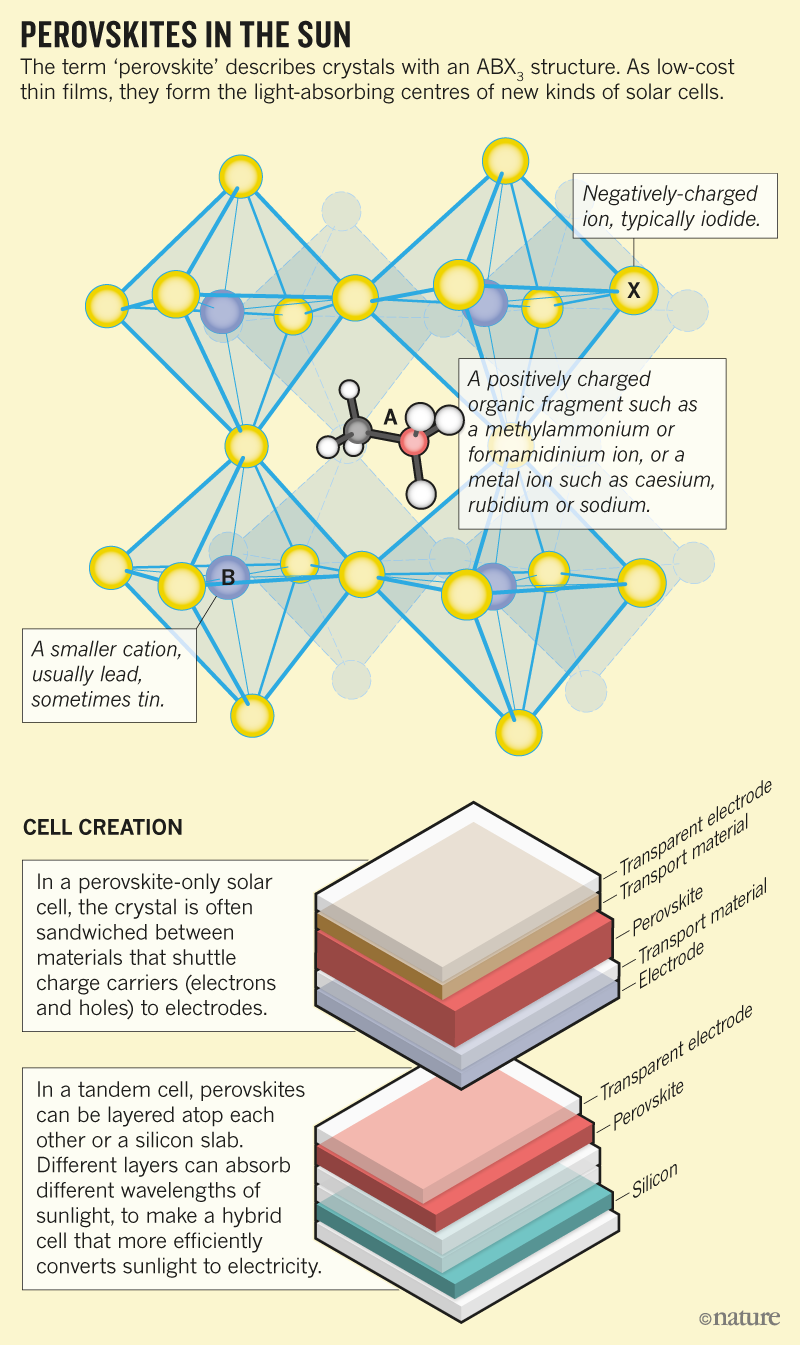
From the perspective of solar power, the important quality of these materials is that incoming light jolts their negatively charged electrons into higher-energy states, leaving behind vacancies, or ‘holes’, that act like positively charged particles. If these charge-carrying electrons and holes can avoid recombining long enough to reach electrodes above and below a perovskite film, then electric current can flow.
The first perovskite photovoltaic devices, reported in 2009, converted just 3.8% of the energy contained in sunlight into electricity. But because the crystals are so easy to make in the lab — by mixing low-cost salt solutions together to form a thin film — researchers quickly managed to improve their performance. By 2018, efficiency had soared to 24.2%, set by researchers in the United States and South Korea — close to silicon’s lab record of 26.7%1. The theoretical limit for both materials is just under 30%, but typical commercial silicon panels hover at 15–17%, with the best around 22%. Unfortunately, perovskite efficiency records are set on tiny samples, smaller than 1 cm2, and the performance doesn’t scale up. The current record laboratory silicon cell, by comparison, measured 79 cm2, and was still 26.6% efficient at 180 cm2 (see ‘Size matters’).
“People haven’t yet demonstrated the ability to make high-efficiency cells in a large-area format,” says Kurtz. One problem is that over large areas, it’s harder to produce uniform coatings. Another is that when working on tiny cells in the lab, scientists collect electric current using transparent electrode films that let a lot of light through, but are also slightly resistive, meaning that they block some current. At larger scales, this resistivity becomes a bigger problem, so commercial cells use electrode films that are more opaque — lowering efficiency. At the multinational electronics firm Panasonic, for example, researchers have reported a 6.25 cm2 perovskite cell with 20.6% efficiency2. But that dropped to 12.6% when 35 cells were combined into a 412 cm2 module3. Microquanta holds the certified world record for perovskite ‘mini-modules’1, with a 17.3% efficient design made from seven cells covering around 17.3 cm2.
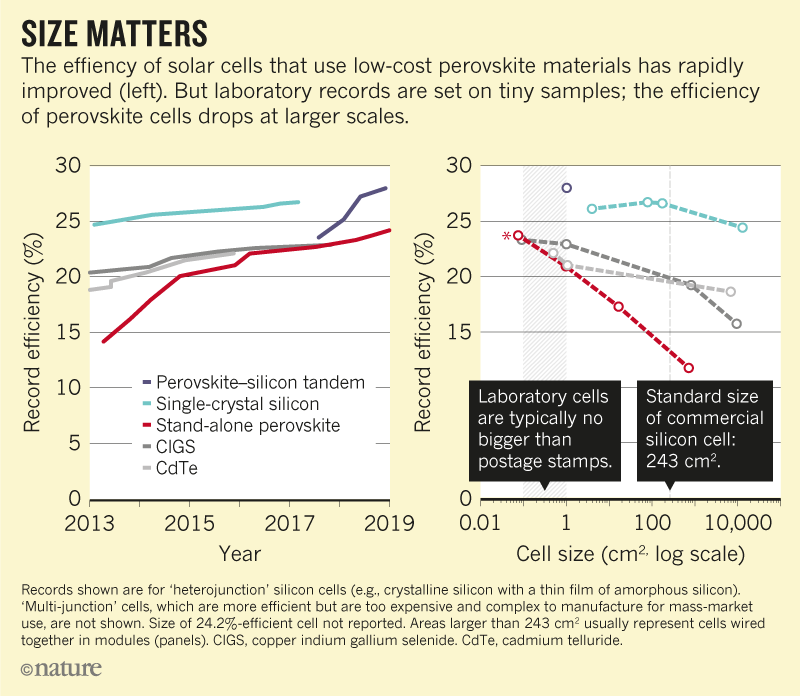
Still, perovskite cells are simpler and cheaper to make than silicon ones are. Silicon production begins by heating sand at 1,800 °C. Making high-purity slabs can include dissolving the material in hydrochloric acid at 300 °C. By comparison, Saule can simply create solutions by using an inkjet printer to deposit tiny amounts of its materials onto plastic films. The company says that it has made moderately large (100 cm2) modules this way, with an efficiency of 10%. Some firms use patterned rollers to apply perovskite inks. And Swift Solar in San Carlos, California, is trying to combine two different kinds of perovskite cells together to create a lightweight tandem module.
But the quickest route to higher efficiency might be to augment silicon with perovskite. Last year, Oxford PV reported a 28% efficient 1 cm2 tandem cell, made by coating a 17%-efficient perovskite layer on top of silicon. Perovskite can absorb more short-wavelength, blue-green light, leaving the silicon to absorb the longer-wavelength, redder light. By the end of this year, the firm aims to produce 27%-efficient commercial-size tandem cells, outperforming the best silicon panels, for its partner companies (which it won’t name) to assemble into modules. These modules will be publicly available by the end of 2020, Case says. Tandems’ theoretical limit is 45%, and a practical goal is 35%, says Case — which would be half as efficient again as today’s best-performing commercial silicon panels.
Will they last?
The major challenge for perovskites, however, is whether they can last as long as silicon panels, which generally come with a 25-year warranty. Perovskite stability “needs to approach the norms established by silicon” and that is “now looking increasingly unlikely”, says Martin Green, who researches perovskites and other solar materials at the University of New South Wales in Sydney, Australia. His team collaborates on the materials with two large Chinese solar-panel makers, Trina Solar and Suntech.
Perovskites are sensitive to air and moisture, but that shouldn’t be a killer problem. Commercial solar panels already encapsulate their photovoltaic materials in plastic and glass for protection. This will probably work for most perovskites, too. A deeper issue lies in the crystals themselves. In some cases, the structures shift as the perovskites warm up; the change is reversible, but it affects performance.
Researchers have worked hard to counter that problem: at the Swiss Federal Institute of Technology in Lausanne (EPFL), a team led by Michael Grätzel has developed structures with three or four different ‘A’ cations in the ABX3 structure. The team combines methylammonium and formamidinium cations with small amounts of caesium and rubidium4, for example. The combination prevents the structural changes driven by temperature and humidity when individual cations are used.
Another issue is that when light shines on perovskite crystals, the small ‘X’ anions can start moving around inside the structures. That can happen if there are any gaps where anions should be, starting a chain of events that can change the crystal’s make-up and efficiency, or lead to device failure. Most solar technologies have some variations in efficiency, says Kurtz. “Perovskites have it in a much bigger way.”
Still, researchers are making progress. “Things have nicely improved,” says Grätzel. In 2017, for instance, his team reported5 0.16 cm2 perovskite cells with more than 20% efficiency and that retained 95% of their performance under full sunlight over 1,000 hours, or 41 days. He says his team has now doubled that time in unpublished work.
Field testing
Most perovskite firms haven’t published their stability results. But they all say that they follow a certification standard established for silicon solar panels, set by the International Electrotechnical Commission (IEC) in Geneva, Switzerland. This standard, known as IEC 61215, involves indoor tests in which modules are heated up to 85 °C for 1,000 hours at 85% relative humidity. The panels are also cycled from −40 °C to 90 °C up to 100 times, and even bombarded with hailstones.
If a silicon panel still works after these tests, it is supposed to have a good chance of lasting 25 years in typical weather. But because perovskites have different instabilities from silicon, they could pass these tests and still fail in the real world. For instance, Microquanta’s perovskite modules passed the IEC 61215, says Buyi Yan, the company’s vice-president. Yet field trials in Hangzhou indicate that the products degrade to 80% of their initial performance in 1–2 years, on average. “Compared to 25–30 years’ lifetime for silicon panels, this is a major shortcoming,” he says. His co-founder, Jizhong Yao, the firm’s chief executive, says newer modules degrade more slowly, but that it’s too early to share details.
Oxford PV’s tandem modules have also passed IEC 61215-level tests, says Case. “Does that mean this is going to last 25 years?” he asks, pointing to a nearby module. “Don’t know. All they are is an indication of long-term durability. They’re a good indication, but ultimately they are insufficient.”
Green says he’ll agree that stability problems have been solved if a perovskite module appears in the top half of an industry scoreboard produced by Norwegian specialist testing company DNV. The firm gets several panels from each manufacturer, puts them through its own set of electrical, optical and temperature tests, and compares results. The tests are similar to the IEC 61215, but are intended to better capture long-term degradation. Perovskite companies are yet to appear on the lists.
Lead toxicity
Another potential stumbling block for perovskite cells is that the best of them contain lead, a toxic metal. Researchers have tried alternatives, such as tin, but performance declines. That doesn’t mean the cells can’t be used. A life-cycle analysis of Oxford PV’s tandem cells suggests that the small amount of lead they contain wouldn’t have much impact on environmental toxicity if it leaked. The analysis also argues that silicon cells have a worse overall environmental impact because of the resources used in their production.
But some researchers say the inclusion of lead rules out the idea of using perovskites in disposable products. Grätzel thinks they might find a use in large solar farms where people seldom go. “If someone wants to sell flexible devices, they have the wrong idea,” he says. “What happens if a kid pierces the plastic cover? There is no compromise on lead toxicity.”
Saule pushes back against that view. Its printed lightweight modules contain very little lead, says Konrad Wojciechowski, the company’s chief scientific officer. Even after encapsulated modules were left soaking in water for a year the level of lead left behind “was still below the World Health Organization limit of lead for potable water”, he says. And Saule’s chief technology officer, Olga Malinkiewicz — who founded the firm in 2014, midway through her PhD — stresses that the products will be robust. “It won’t be possible for a child to disintegrate and delaminate a perovskite panel accidentally,” she says.
Cheaper solar power?
For perovskite firms that hope their products will reduce the costs of solar power, there’s another problem: silicon panels are already cheap, and the price is dropping. “While I find the solar sector more exciting than ever, it does not need a tech breakthrough,” says Jenny Chase, head of solar analysis at BloombergNEF in Zurich, Switzerland. “It’s one of the cheapest sources of electricity in many countries already. Crystalline silicon technology is good enough, and it’s hard to beat. Perovskites might eventually shave a few cents per watt off the cost, but they’re not something we need to wait for.”
Case disagrees. His company’s tandem modules will cost more than silicon ones, but the greater efficiency will reduce costs of generating solar energy by 17–23% in a few years, he argues. That prospect has piqued the interest of some large companies. In March, Oxford PV secured £31 million (US$39 million) from firms including Chinese wind-turbine manufacturing giant Goldwind; in total it has raised £76 million.
Meanwhile, most firms producing perovskite-only modules say they don’t expect to enter the mainstream solar-panel market — at least, not immediately — which is why they are focusing on lightweight films. Saule wants to sell flexible single perovskite layer solar films in 2021, and Tokyo-based Sekisui Chemical, the second-largest holder of perovskite patents after Oxford PV, plans to sell flexible cells in 2020. It’s involved in a large consortium with Panasonic and fellow Japanese electronics giant Toshiba.
Some companies have already bailed out of the perovskite market. Multinational photography firm Fujifilm is the third-largest holder of perovskite solar patents. But after doing fundamental research on perovskite solar cells, it is no longer developing the cells or materials used to make them, says spokesperson Shohei Kawasaki. And Australian perovskite developer GreatCell Solar went into administration in December; it failed to attract enough investment to build a prototype facility, even though it had struck up a partnership with one of the world’s largest solar-panel manufacturers, JinkoSolar in Shanghai, China.
These setbacks hint that the benefits of perovskites aren’t as easy to reap as advocates hoped. And they underline the importance of the outdoor trials. Many more of these are needed, says Grätzel, who recalls visiting the test site of the Chinese firm WonderSolar, in Ezhou, last summer. “The outside temperature was 28 °C, but the panels were at 70 °C. I was sweating, and the panels were too,” he says. “Let’s see how they fare.”