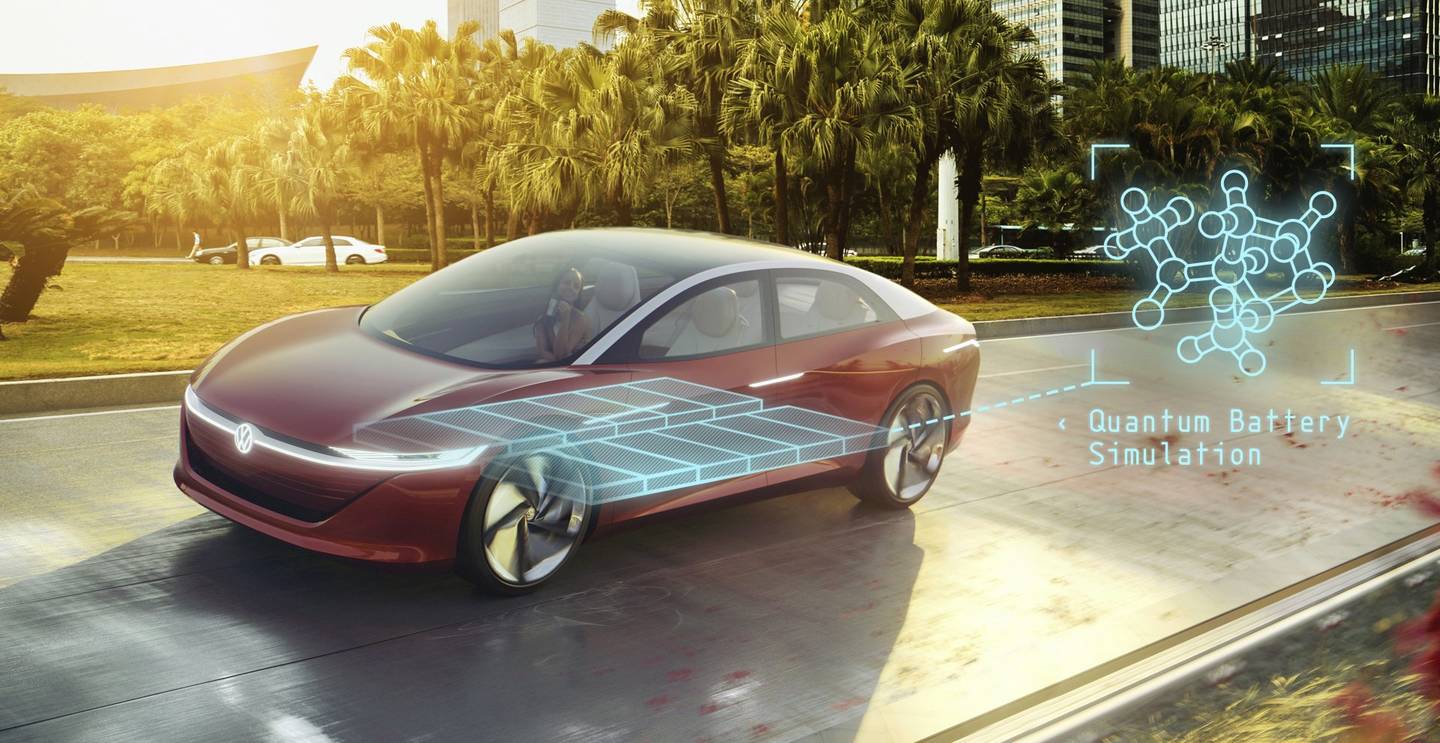
In the quest for a next-generation battery to power gadgets and electric cars, the lithium metal battery is a top contender. It has a negative electrode made of pure lithium, and promises to more than double the energy-storage capacity of today’s batteries. But lithium metal batteries easily catch fire, and they last just a few hundred recharge cycles. Now, by concocting a concentrated, fire-retardant electrolyte, researchers have taken a big step towards safer, long-lasting lithium metal batteries (Joule, 2018. DOI: 10.1016/j.joule.2018.05.002).
The new electrolyte does not ignite when exposed to a direct flame. And battery cells made with it retain their storage capacity after being recharged 600 times, “one of the best results for any lithium metal battery,” says Ji-Guang Zhang of the Pacific Northwest National Laboratory, who led the new work.
Today’s lithium-ion batteries last for around 1,000 recharge cycles. They typically use a graphite anode and lithium cobalt oxide cathode. The electrolyte is a 1 M solution of lithium salts in flammable organic solvents. Their energy density maxes out at 200–250 Watt-hours per kilogram. The U.S. Department of Energy wants to double this to 500 Wh/kg. That would mean compact batteries for wearables or cars that can drive much longer on a single charge.
Lithium metal batteries could in theory meet that goal. That is why researchers explored lithium metal anodes back in the 1970s. But loose, uneven metal deposits on the anode create spiky dendrites that can reach the cathode and short circuit the battery, sometimes igniting the flammable electrolyte. Plus, metal anodes react with the electrolyte, consuming both and cutting battery life short.
Many groups are exploring solid polymer or ceramic electrolytes as an answer. But those do not conduct ions well, and the interfaces between solid electrodes and electrolyte have poor contact.
Zhang and his colleagues instead turned to highly concentrated electrolytes. In viscous lithium salt solutions, the salt and solvent react with lithium to create a micrometers-thick, densely packed layer of knobby lithium granules on the anode when the battery is charged the first few times. This solid layer prevents dendrites and keeps the lithium metal anode from further reacting with the electrolyte, boosting the battery’s cycle life and safety.
Because lithium salts are expensive, the PNNL team reduced the salt needed by making a novel electrolyte that contains small concentrated clusters of lithium salts in solvent. First they make a concentrated 3.2 M solution of lithium bis(fluorosulfonyl) imide in triethyl phosphate, a known fire-retardant solvent. Then they dilute it with a fluorinated ether to make a 1.2 M solution.
The ether does not react with the salt, so the diluted electrolyte contains highly concentrated salt-solvent clusters. The clusters maintain the ability to form the dendrite-tamping solid lithium layer on the anode. Glass fibers soaked with the new electrolyte solution could not be ignited in tests where conventional electrolytes immediately caught fire.
However, there’s a lot more to be done. Batteries made with a lithium metal anode and the new electrolyte have an energy density of more than 300 Wh/kg, better than today’s batteries but still not close to the DOE benchmark.
Nevertheless, says M. Stanley Whittingham, lithium-ion battery pioneer and chemist at the State University of New York at Binghamton, “this is very important work that may help us move away from bulky graphite anodes.” Thin lithium foil anodes could potentially make batteries compact and flexible. Although solid-state batteries promise the same reward, they are a completely new approach and could be slower to adapt to a large scale, he says. “This is essentially drop-in technology, so the present manufacturing methods and facilities can be used.”